Learn how Safety Data Sheets (SDS) play a critical role in OSHA and WHMIS compliance. Discover key differences, shared principles, and best practices for regulatory success.
Table of Contents
- Introduction
- Overview of SDS, OSHA, and WHMIS compliance.
- Why SDS is a critical link in regulatory frameworks.
- What Is OSHA Compliance?
- Brief explanation of OSHA and its importance in workplace safety in the USA.
- How SDS fits into OSHA’s Hazard Communication Standard (HCS).
- Understanding WHMIS
- Introduction to WHMIS (Workplace Hazardous Materials Information System) in Canada.
- The role of SDS in meeting WHMIS regulations.
- The SDS as a Bridge Between OSHA and WHMIS
- The shared principles of OSHA and WHMIS under the Globally Harmonized System (GHS).
- How SDS ensures a unified approach across borders.
- Key Differences Between OSHA and WHMIS
- Comparison of regulations under both systems.
- What businesses operating in both countries need to know.
- Why Accurate and Up-to-Date SDS Matter
- Risks of non-compliance: penalties, legal action, and workplace accidents.
- Best practices for maintaining SDS to stay compliant.
- Leveraging Digital Tools for Compliance
- How digital SDS management systems streamline OSHA and WHMIS compliance.
- Features to look for in a good SDS management tool.
- Conclusion
- Reinforcing the importance of SDS in regulatory compliance.
Introduction
Safety Data Sheets (SDS) are the backbone of workplace safety regulations in the USA and Canada. These documents ensure that employees and employers have access to critical information about hazardous materials, enabling safer handling and storage. SDS also serve as a key component in compliance with OSHA (Occupational Safety and Health Administration) and WHMIS (Workplace Hazardous Materials Information System). This blog dives into how SDS support these regulatory frameworks, their shared principles under the Globally Harmonized System (GHS), and why they are vital for cross-border compliance.
What Is OSHA Compliance?
OSHA, the United States’ workplace safety watchdog, sets the standards for protecting employees from chemical hazards. One of its most critical regulations is the Hazard Communication Standard (HCS), which mandates that manufacturers, importers, and distributors provide accurate SDS for hazardous products.
SDS ensures that employees are informed about:
- Chemical properties.
- Potential hazards (health, fire, and reactivity).
- Safety precautions for handling and storage.
Failing to comply with OSHA’s SDS requirements can result in steep fines and jeopardize workplace safety.
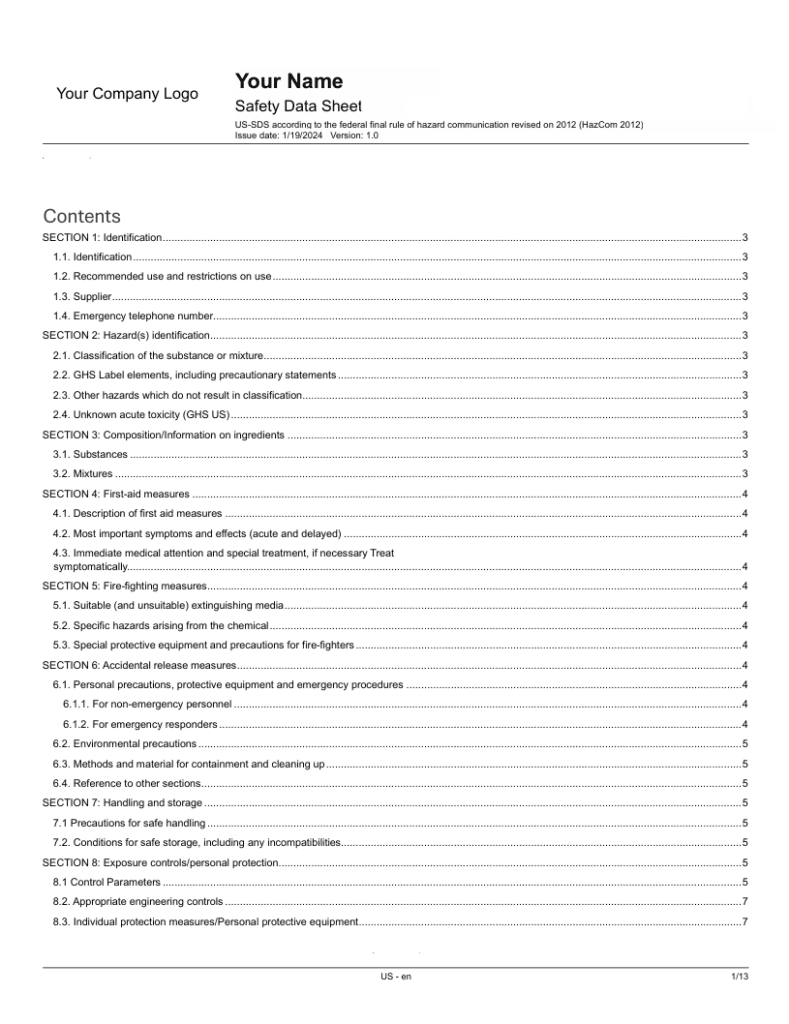
Understanding WHMIS
In Canada, WHMIS governs the communication of hazardous materials in workplaces. It mandates that all hazardous products come with an accurate SDS to inform workers about potential risks and safety measures.
Key components of WHMIS include:
- Supplier and workplace labels.
- SDS with 16-section GHS formatting.
- Employee education and training.
By providing comprehensive information, WHMIS empowers employees to minimize risks and respond effectively to emergencies.
The SDS as a Bridge Between OSHA and WHMIS
Both OSHA and WHMIS are grounded in the principles of the Globally Harmonized System (GHS). This ensures a standardized approach to chemical classification and labeling, making SDS consistent across borders.
For businesses operating in both the USA and Canada, a GHS-compliant SDS simplifies compliance with OSHA and WHMIS regulations, reducing duplication and ensuring uniform safety practices.
Key Differences Between OSHA and WHMIS
While OSHA and WHMIS share common principles, there are notable differences:
- Scope: OSHA focuses on employee safety in the USA, while WHMIS extends to environmental considerations in Canada.
- Training Requirements: WHMIS mandates specific training tailored to workplace hazards, while OSHA emphasizes hazard communication.
Understanding these differences is critical for businesses operating internationally.
Why Accurate and Up-to-Date SDS Matter
Non-compliance with OSHA or WHMIS can lead to:
- Legal penalties and fines.
- Workplace accidents and injuries.
- Damaged reputation and customer trust.
To stay compliant, businesses must:
- Regularly review and update SDS to reflect current regulations.
- Ensure accessibility for employees and stakeholders.
Leveraging Digital Tools for Compliance
Digital SDS management systems streamline the compliance process by:
- Providing centralized access to SDS for employees.
- Sending automated reminders for updates.
- Offering GHS-compliant templates for consistency.
Choosing the right tool ensures that your business stays compliant and reduces administrative burdens.
Conclusion
Safety Data Sheets are more than regulatory paperwork; they are a critical element of workplace safety. By ensuring OSHA and WHMIS compliance, businesses protect employees, avoid legal risks, and build trust with customers.
Take the next step to simplify your compliance journey with ICSDS—explore digital SDS management solutions tailored to your needs.